After travelling to Hamilton and seeing first hand how wood type was created in the early 1900’s I have been looking at ways to use modern technology to do similar things. Having previously looked into laser cutting in the past I now wanted to experiment with the emerging 3D printing technology. With 3d printing becoming affordable and accessible to a (albeit pretty geeky) layman as myself it seemed like now was a good time to experiment.
Different 3D printers work in different ways, some using plastics and some using lasers to create their magic. The machine I used heats up a plastic filament and extrudes a 0.3mm thick string. It builds up hundreds and hundreds of these into layers. My previous research into the technology lead me to believe this could be a great way to make new type.
One of my main frustrations with researching new type creation methods is bringing the newly cut/made type up to type height. If you are laser cutting or routing a new block of type you either need to have a custom made strip of wood prepared at the correct printable height (0.918 of an inch) or you need to cut the type into a thin substrate and then mount it on another block. Even then with this method you would probably have to pad it up with card or paper due to most substrates coming in millimeter thicknesses.
3D printed type would avoid this as you could print an entire block and letter in one go to the correct height. With a 3D printed object you can adjust how hollow the object is (called infill). Due to the nature of the printing (imagine having a sack of icing that you are piping onto a cake as it’s a similar method) the inside of the object can be filled with a criss-crossed honey comb pattern to save on material. This creates a suprisingly light but strong object.
Although in the future I want to experiment with this process to create all new type and forms that are informed by the printing process, for the first test I went with something really basic – an Inch high capital Helvetica “A”.
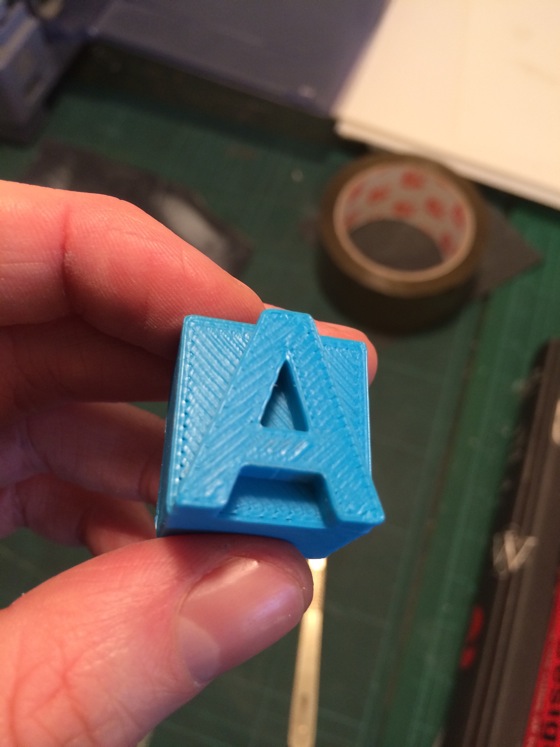
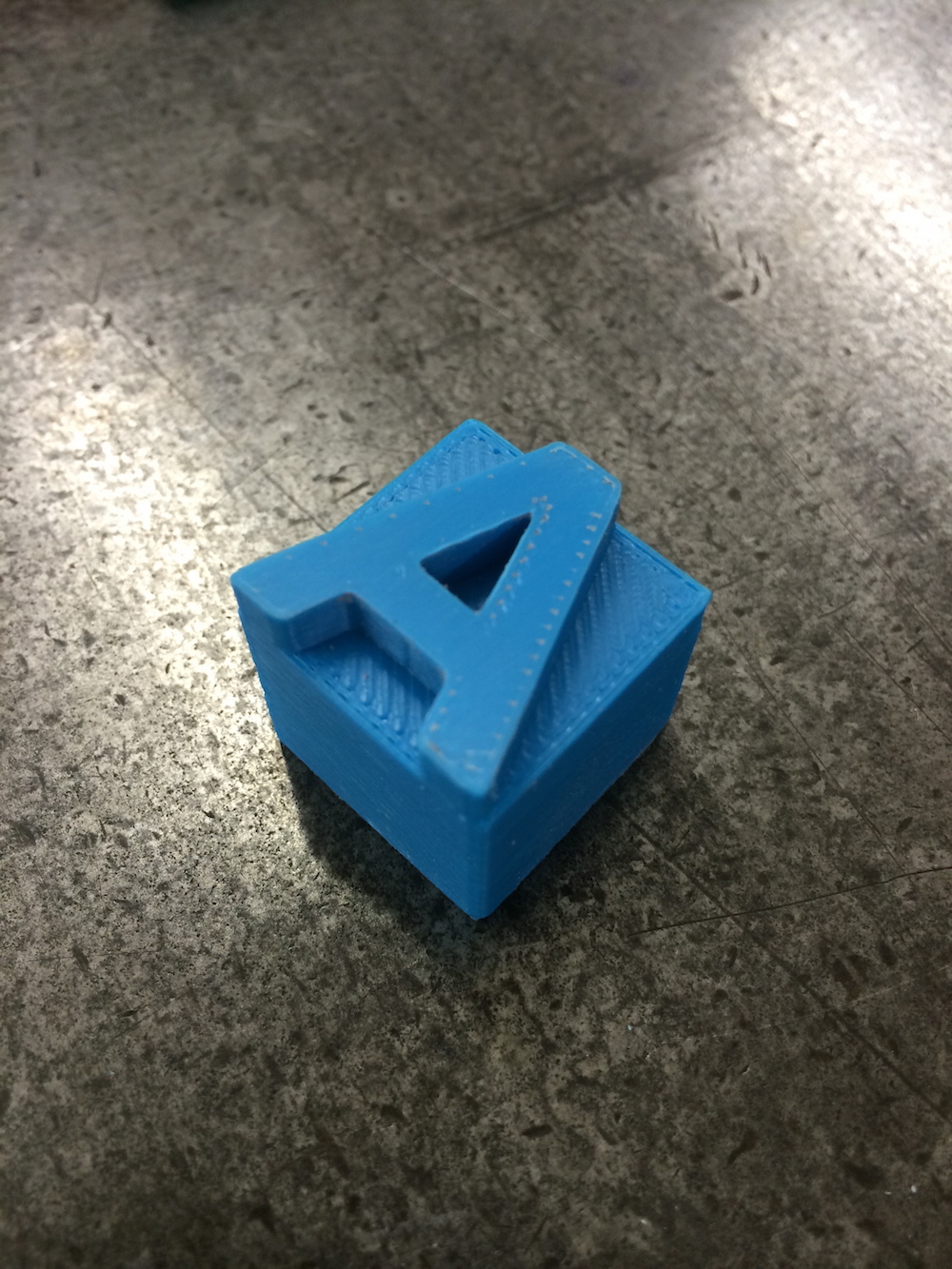
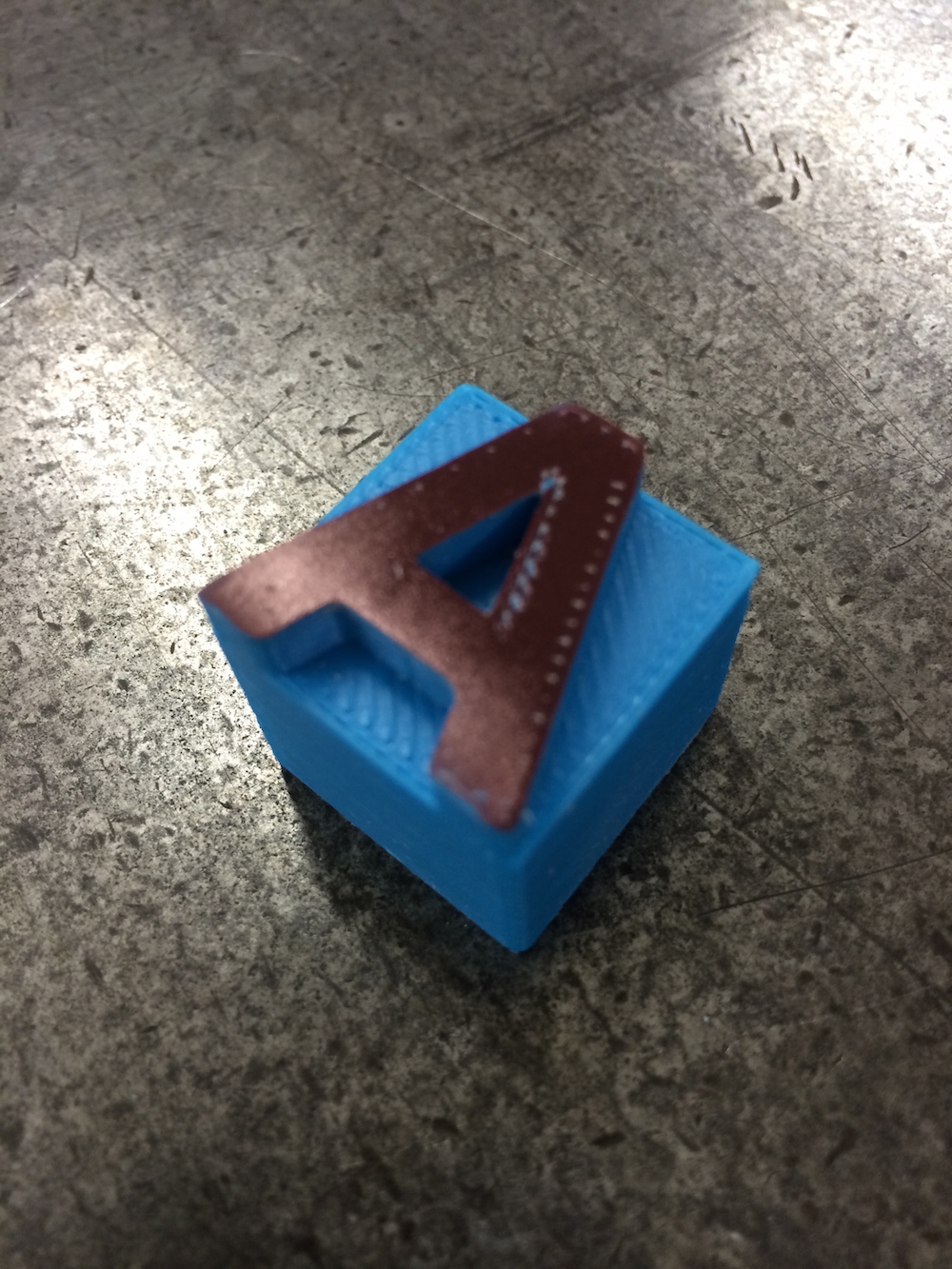
Once the printer has finished the block has a slight texture to the top surface, caused by the print nozzle filling in the surface. In the future I’ll try printing this surface but for the moment I gave it a very light sanding with wet/dry paper to give it a smooth, printable surface.
The type inked up well, giving an even coverage. You can just able see here the slight gaps in the surface of the type. As I said as the nozzle is prinitng the surface it has trouble getting right up to the edges, as the extruded plastic and nozzle are circular when it hits a flat edge it goes as far as it can before looping back on its self. In the future I’m going to investigate ways that I can either fill and then sand the surface to prevent this or possible adjust the settings of the printer to accomodate for it.
In general I was really impressed with the print quality of the block. At the bottom of this image the two blocks I made have been printed next to a wooden block and as you can see the results are promissing. A consistant application of ink in a similar density to that of wood. My type is slightly smaller than it as one of the print size settings was input wrongly so technically this type is 70pt rather than 72pt. The “filled” and “hollow” scrawled next to the prints indicates the two different methods I used when printing them. The “filled” one has a honeycomb filling whilst the “hollow” one has a void engineering into the centre of it to see whether that affected the weight, printing time or print quality. The difference between them was negligible, the variance around the edges of the “hollow” on is where I sanded it slightly too much.
All in all I think this techique could create some very interesting new avenues for either new type creation on in some cases perhaps duplicating/filling in missing letters to fonts I already have. At the moment I am developing a whole new type face that will be based around the strngths and weaknesses of the printing methods. More than anything I would like the resulting typeface when printed to have elements of it’s creation evident within it, either with the design being influenced by the printing method or in the type actually showing the layers that it is made from in some way (similar to the way wooden type shows the wood grain).